SiCAST – The influence of SiC raw materials on the performance of refractory castables in waste and biomass incineration
Laufzeit: 01.03.2019 - 28.02.2021
Partner: INISMa - INstitut Interuniversitaire des Silicates, Sols et Matériaux, FGF - Forschungsgemeinschaft Feuerfest e. V.
Förderung durch: BMWi über AiF-Cornet
Projektmittel (€): 250.000
Kurzfassung
SiC containing castables as typically used in incineration of waste and biomass suffer of a lack of strength in the temperature field of 800 to 1350 C. This low temperature range is typical for biomass combustion like waste incineration and pellet heaters for private households but also for CO2-neutral power and heat generation in industrial scale. In the temperature range of 800 to 1350 C hydraulic bond SiC castables are characterized by a weak strength, because the dehydration process...SiC containing castables as typically used in incineration of waste and biomass suffer of a lack of strength in the temperature field of 800 to 1350 °C. This low temperature range is typical for biomass combustion like waste incineration and pellet heaters for private households but also for CO2-neutral power and heat generation in industrial scale. In the temperature range of 800 to 1350 °C hydraulic bond SiC castables are characterized by a weak strength, because the dehydration process already destroyed the hydraulic bonding phase. However, in this temperature field no sintering of the castable matrix components lead to a significant strength. Due to the grain shapes of SiC that typically forms well de-veloped crystal faces the grain matrix interlocking is poor but in terms of use essentially for a proper strength evolution. In further SiC is sluggish in reaction in the said tempera-ture range that avoids a proper formation of a ceramic bond.
On the other hand, SiC has been identified as a material that has an outstanding corrosion resistance against alkaline rich vapours that typically occur when biomass is combusted and due to its good thermal conductivity SiC containing materials are less sensitive to thermal stress.
With increasing SiC content in the castables the resistance to thermal shock and gradient is significantly improved. Therefore, on the one hand the corrosion resistance and thermo-mechanical properties are systematically improved with increasing SiC content. On the other hand, SiC is sensitive to oxidation, that even get worse if water vapour is present.
However SiC containing castables are inevitable in the said field of application as repair mixes of for the construction of complex structures. The use of SiC castables in further reduces significantly reduces downtimes of said combustion units.
Therefore, the purpose of this project is the:
• improvement of the strength in the typical temperature field of use (800 to 1350 °C),
• improvement of corrosion resistance against sulphur, H2O and alkalines.
• consolidation of knowledge about the chemical and mineralogical reaction of SiC with further castable components and the ambient atmosphere that is present in combustion units.
The shortcomings of the present state of art are:
• poor endurance of SiC castables in comparison to SiC bricks that even got worse due to increasing incineration temperatures from 1200 to 1350 °C over the last years.
• no systematic investigations how SiC influence the material properties, as a func-tion of SiC content and ambient conditions.
• lack of microanalytically methods for precise investigation of the interaction of SiC with further castable components and the ambient atmosphere.
• improper testing setup for corrosion against gaseous components (SOx, CO2, alka-lines).» weiterlesen» einklappen
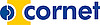